Cooling Tower Concrete Repair Phoenix
Even with the best mix and pour concrete deteriorates over time. Reinforced concrete structures require continual maintenance and inspection. This helps find and repair small issues before they compromise the entire structure. Structural elements of the cooling towers are many times made of concrete. Concrete can comprise the foundation, housing for mechanical elements, and even be the liquid containment area. Deterioration occurs in both mechanical draft and natural draft technologies. How quickly the deterioration occurs in these aggressive environments is dependent on regular maintenance. It is also affected by the consistency of the processes. If the processes shift drastically, it can also reduce cooling tower concrete life. This is based on the assumption that the cooling tower’s concrete elements were constructed using the best practices.
Unfortunately for the end user and responsible party for maintaining cooling towers the quality of initial construction plays a very large role in the lifespan of the cooling tower. In addition exposure to unusually harsh chemicals or environmental exposure can accelerate deterioration. Which can lead to structural failures and complete rebuilds or replacements. A quality assessment of the structure will help understand any deficiencies in the structure. Along with an understanding of the cooling tower’s individual environmental load from weather and chemical exposure can help develop deterioration trends. Knowing the current condition and the projected deterioration schedule helps owners project their maintenance costs and cooling tower costs over longer periods of time.
Adequate preparation for the future is the key to successful business. For private companies or public municipalities it is critical to have a plan in place to prepare for all costs. Proper evaluation, investigation, and planning will help understand and plan for the life-cycles of cooling towers. Many owners and civil divisions use an LQQ method for understanding and planning for their assets. This can simplify and make planning maintenance much easier and more effective. An LQQ system means Locating, Qualifying, and Quantifying the condition of the concrete structure. Once the root-cause issues are identified planning can be made to regularly maintain and extend the serviceable life of the concrete cooling tower. This makes the budgeting for these eventualities realistic and avoids surprise maintenance issues that can be fairly costly.
Original Cooling Tower Construction
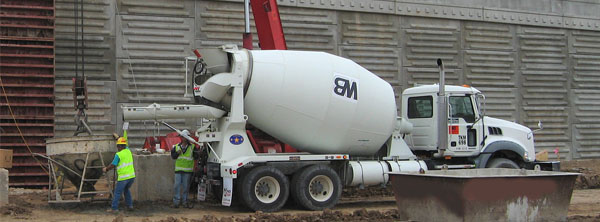
The costs of conducting effective quality control and quality assurance during the construction phase of concrete cooling tower elements is absolutely critical to the lifespan of the cooling tower. Documentation can be made during the construction phase, yet without visually inspecting during the actual construction there is little assurance that it is being done correctly. The ways that construction mistakes or failures can manifest are varied. Here’s a list of common issues during cooling tower construction.
- Ignoring manufacturer recommendations with regard to construction and application methods.
- Failure to accurately follow the original construction documents.
- Substitution of inferior materials.
- Inaccurate or inappropriate materials specified for construction.
- Substandard construction documentation
- Damage or abuse to the structure during the original construction process.
- Inferior craftsmanship during construction.
Unfortunately many of the defects in the construction process manifest themselves in obvious visual failure until after negotiated warranty periods. This leaves owners or municipalities stuck having to maintain inferior concrete. Maintenance that is far more involved and costly that what is normal wear and tear on the concrete elements of cooling towers. Incorporating the walk through lists that are carefully followed by qualified construction professionals during the concrete construction phase is fundamental in catching and addressing original construction problems.
Simply seeing and fixing a problem area in the concrete isn’t a total repair solution. Owners need to ask for and get root-cause assessments that point to the root reason the concrete is failing or deteriorating more quickly. This will point out a potential quality and longer lasting repair solution. This avoids putting a series of “band aid” repairs on top of each other.
Planning Scheduled Cooling Tower Maintenance
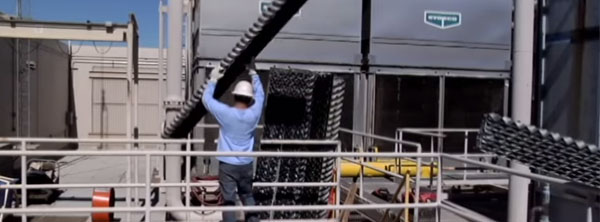
Even if the cooling tower’s concrete is built to specifications everything degrades over time. When a cooling tower in installed a plan should be put in place for the inspection and regular maintenance. This makes predicting expenses easier. It also ensures that the inspections, preventative maintenance and repairs are actually carried out. Many times downtime for the cooling tower is limited and maintenance must be done quickly. During these downtimes deterioration may be noted but not acted upon. These reports are critical in preparation for following scheduled maintenance. Extra time should be scheduled for the repair of any problem areas. The type of damage or issues that might be noted regarding the reinforced concrete structure might include;
- Joint sealant failures
- Wall or base slab cracks that leak water
- Deterioration and/or leaking from expansion joints
- Mechanical penetration leakage
- Deficient foundation support for the cooling tower
- Corrosion of the anchor bolts
- Spalling or corrosion of embedded concrete rebar
- Vegetation or algal growth in the cooling tower
- Deterioration of surface paste or coatings
Each cooling tower structure poses unique obstacles for cooling tower repair contractors. An engineered solution is a must to address each of the issues fully. This is true for both minor and major structural issues. Whether the problem is a crack, foundational stabilization issue, deteriorated containment liner, or halting cooling tower water egress a proper repair strategy should include the following.
- Inspect and identify the root cause
- Use the right techniques and raw materials in repair
- Employ a quality control program for the repairs
- Hire only qualified and experienced cooling tower repair contractors
Assessing Concrete Deterioration
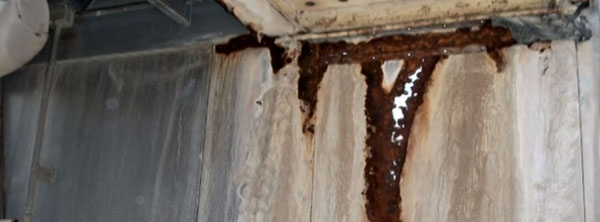
During the regularly scheduled maintenance it is the responsibility of cooling tower crews to watch for, note, and report any deteriorated sections of the cooling tower. If issues are found a structured assessment should be done. The approach for that evaluation should follow this pattern.
- Find the deteriorated area
- Determine the root cause and affected elements
- Determine what repairs are needed
- Weigh repair vs. replacement for these repairs
One the damage or deterioration is accurately assessed, a detailed and through repair plan be developed. This plan will include variables relevant to each cooling tower’s particular operating environment. It will take into account all of the variables that affect the cooling tower and its concrete. The chemical, construction material, and thermodynamic variables that affect cooling towers should be addressed specifically. This approach should produce a longer lasting repair plan that will increase the serviceable lifespan of the cooling tower.
Quality Cooling Tower Concrete Inspection & Repair
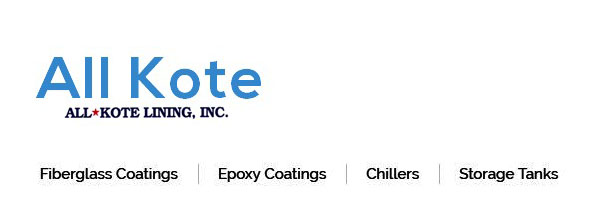
If your cooling tower concrete is showing signs of failure, or if you want to develop a quality maintenance plan All Kote can help. Having a accurate idea of the condition of your cooling tower concrete elements helps with budgeting and avoids unnecessary surprise costs. Call All Kote today to get your appointment scheduled at 480-966-4446.